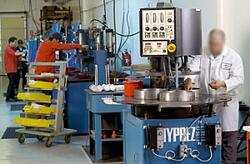
Most of you have a good grasp on what “lapping” means, but there remains a lot of confusion about what exactly lapping is and why we need it. Fully understanding the process and its value can be beneficial for personnel throughout the supply chain.
So what is lapping? It is a free abrasive machining process which removes material at a controlled rate. At Centerline, we can finish pieces without introducing the stresses and heat damage associated with some other processes. We have gone into greater technical detail about the process on our lapping page.
What are the benefits of lapping? The main reasons to utilize precision lapping services include control over thickness identity, surface finish, part uniformity, flatness, camber reduction, parallelism and preparation for polish. You can find brief explanations for each below.
1. Thickness Identity-
Lapping allows for much tighter thickness tolerance. Raw materials that have been dry pressed or tape cast, often referred to as “as-fired”, typically have a thickness tolerance of 10%. Standard lap thickness tolerance is +/-.0005”/” and can be as tight as .00005”/” depending on the length, width and thickness of the part or substrate.
2. Surface Finish-
The surface finish of as-fired materials is usually specified in micro-inch max parameters. As a result, the manufacturer can get away with large surface finish variation within batches. Our various abrasives and unique proprietary processes allow for better control over the finish.
It’s important to note, however, that the surface finish is dictated to some degree by the material’s structure or grain size. For specific information on a material’s capabilities either request a quote from us or email technical support specifying the material and surface finish desired.
3. Part Uniformity-
As we all know, having uniform parts is crucial for producing repeatable results. Precision lapping provides excellent control to ensure uniform pieces within specified parameters.
4. Flatness-
Lapping controls the flatness of your parts or substrates. For information on flatness keep your eyes peeled for our upcoming article on camber, flatness and parallelism or contact us with questions.
5. Camber Reduction-
Precision lapping aids in the removal of deviation, bow and warp on a substrate. Typical substrates in as-fired condition have camber specifications of .002” to .003” inch per inch. Lapping or polishing substrates will decrease camber to .0005”/”.
6. Parallelism-
Achieving parallelism between faces on a substrate can be very important. Lapping is a great way to guarantee parallelism to extremely tight tolerances.
7. Preparation for Polishing
Precision lapping is used in the preparation of any part or substrate to be polished. The parts go through various lapping abrasives to reduce the subsurface damage before moving on to the precision polishing process.
Now that you know the many benefits of precision lapping, be sure to contact us with any questions or head on over to our lapping page for more information on our processes.